Layered process audits: company layers in sight
Layered process audits are a key to sustainable process optimisation
One of the fundamental requirements in many companies is to ensure process standards in order to provide customers (including internal ones) with a ‘thing’ that basically everyone always buys (and wants to have) without this being the explicit content of any form of service description or similar.
This one ‘thing’ is a repeated promise of performance that also applies to unique items and basically even to works of art. If I want to buy a van Gogh (assuming he was still alive and painting), then I have a certain idea of the style on which he is based and would probably not be satisfied with a Dali or Rembrandt.
Based on this promise of repeat performance and the necessary process standards, the question arises as to how this can be continuously ensured. This is where layered process audits come into play.
The emergence of layered process audits
Layered process audits (LPA) emerged in the automotive industry in the early 2000s and are now used by practically all OEMs and their suppliers.
The fact that this involves processes (and their standards) is already expressed in the name. The fact that there are checklists behind the audits (the plural is an important aspect) should not really come as a surprise. However, the form and handling of these checklists does, which is why this will also be a topic of this article.
The term ‘layered’ expresses the fact that process audits are carried out at different levels of the company hierarchy. It is also possible to use LPA in a purely process-oriented form of organisation; instead of referring to hierarchical levels, it is then mapped to performance, support and management processes.
The central question behind layered process audits always revolves around compliance with defined process standards at a certain level, but also below. The lowest level is always the level of value creation, i.e. the level at which a correct, i.e. error-free change to an item (product or service) takes place at the first attempt, which creates a benefit for the (one!) customer and for which they are therefore prepared to pay. In the case of support processes (e.g. logistics, purchasing, IT, HR, …), the corresponding service process must typically be viewed as an internal customer and therefore a certain detachment from monetary remuneration must also be taken into account.
Checklists and checkpoints
First of all, the good or bad news, depending on how you look at it: With one exception, there are no standard checklists for layered process audits, not even standard checkpoints (there is one exception).
This may sound very strange at first in the context of process standards, but the further explanations will show why this is a great advantage and what benefits arise on another level.
Let’s start by taking a look at the one standard checkpoint:
At the subordinate level, the Layered Process Audit was carried out as planned and, if necessary, the corresponding measures were initiated.
Simple, right? We look from one level to the level below and check whether the LPA has been carried out. This is almost trivial and doesn’t hurt.
If we take a closer look at this checkpoint, what is the first thing we recognise?
Correct, it is a closed question or statement to which there can only be a positive or negative answer. This is a central principle for all checkpoints and therefore also for the checklists: they are always closed questions or statements so that there are no unnecessary discussions about whether a checkpoint is 70 % or 90 % fulfilled (and therefore everything is not so bad and you can go back to business as usual). It’s always all or nothing, positive or negative.
If the answer is positive, everything is fine and the checkpoint is visually marked with a green dot. If the answer is negative, there are now various cases:
- The subordinate audit was carried out, but not as planned. This response does not in itself result in any further action, except perhaps a reminder and possibly an enquiry to the person responsible as to the reason for this and what might need to be changed so that the audit (and all further rounds) can be carried out as planned. This ‘what needs to be changed’ could be a possible follow-up measure, the effectiveness of which is then checked during the next audit. The checkpoint itself is set to yellow, as the subordinate audit has already been carried out.
- The subordinate audit has not been carried out. There are now other possible subordinate cases.
- As an immediate measure, the subordinate audit can be carried out immediately. The checkpoint is then also set to yellow and is thus completed for the time being.
- The subordinate audit cannot be carried out immediately. The reasons for this can be very different in nature and are basically irrelevant, except that a suitable measure is derived from this. In the simplest case, it could be that the checkpoint (i.e. the check for the implementation of the subordinate audit) is simply postponed to the next run (but should only be done once). Or considerations and a derived measure could take place, as described above under 1. However, the checkpoint is set to red for clear differentiation. This red marking indicates that the checkpoint has not been completed and a follow-up action has been initiated that could not be completed immediately.
- The red checkpoint mark is also assigned if it is recognisable during the review of the subordinate checklist that no appropriate measures have been initiated there.
Essentially, that’s it as far as the basic handling of checkpoints is concerned.
And where do the checkpoints come from?
Now only one question remains: Where do the other checkpoints come from?
Essentially, these checkpoints come from the process standards mentioned at the beginning. In the event that these are unknown or non-existent, you have another checkpoint (‘process standards are available and known’) and the measure is delivered straight away.
If the process standards are in place and known, there may of course still be cases in which they are not (or cannot be) complied with. In this case, too, the measure is virtually self-evident (‘Change the process standard or the context so that it can be complied with’). Depending on whether the measure can be implemented immediately, i.e. during the audit, the checkpoint is marked yellow or red.
Another source of checkpoints can be customer complaints (also from internal customers). This is usually an indication that the current process standard is not as effective as it should be. This in turn can point to the process itself or its context.
In addition to these general topics, other sources of checkpoints can also be sector or industry-specific standards, e.g. in the industry from the area of safety, order, cleanliness (the famous 5S), as well as regulatory requirements for data protection, data security, sustainability, etc. As a rule, these are always areas that cannot (yet) be automated or whose automation is not worthwhile due to the uniqueness of the processes.
Goals and added value of layered process audits
The basic aim of layered process audits is to only ever receive green ratings for the checks, with the yellow checks disappearing at some point and the measures for the red checks becoming effective.
This can then go so far that green checkpoints eventually disappear from the checklists, simply because the corresponding process standards are perfectly adhered to. The bad news here, however, is that the checkpoints for subordinate audits always remain, but this is negligible in the consistently positive case (then audits are actually really fun 😉).
So that it doesn’t get boring, you can (should!) always ensure that the process standards are further improved (better, simpler, faster, cheaper, …). Typically, this leads to problems again and new checkpoints are delivered free of charge.
As layered process audits are typically carried out by the responsible managers, the introduction of LPA is also an excellent means of bringing managers above the lowest level to the point of value creation (as this is where they find the results of the subordinate audits). This creates a deep understanding at all levels of the value chain, the standards required and the opportunities to improve these standards.
At the same time, the layered process audits are accompanied by intensive communication between managers and employees, which automatically becomes necessary in order to jointly implement immediate measures to achieve the process standards or to initiate further measures.
Finally, the communicative aspects of layered process audits should also be taken as an opportunity to point out that the aim is not to turn the people involved into mindless machines, but to give them the freedom to deal with unexpected events and deviations through appropriate routines and habits, while still complying with standards that ultimately bring the benefits mentioned at the beginning.
Conclusion
The major difference between layered process audits and all other classic audits is the way in which the highly dynamic checklists are handled. In addition, the inclusion of the entire organisation across all hierarchical levels or, alternatively, the entire process landscape across all performance, support and management processes is also special. The price for this is that there are initially no ready-made checklists. At the same time, this has the great advantage that you still have to familiarise yourself intensively with the process standards in order to derive initial checklists from them.
Compared to traditional audits, LPAs have the major advantage that they make the necessary checks a natural part of day-to-day operations (including in management at all levels) and prioritise the immediate elimination of deviations instead of putting this off until the next annual or even less frequent audit date.
References and recommended reading:
We are happy to recommend two other German sources for further reading on this topic:
- Warum Lean Hintertueren braucht
- Elmer Zeller: Layered Process Audits
Would you like to discuss Layered Process Audits in more depth? You can easily reach Götz Müller via his website or on LinkedIn.
If you like the article or would like to discuss it, please feel free to share it with your network.
Götz Müller has published more posts on the t2informatik Blog:
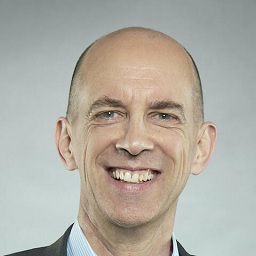
Götz Müller
Goetz Mueller has been involved in the management of development projects since 1993, change projects and continuous improvement processes since 1998 and Neuro-Linguistic Programming since 2006. He is a trained Lean Facilitator, Lean Six Sigma Black Belt and NLP Master Practitioner. Since 2009, he has been working as an independent consultant, trainer and coach, supporting small businesses, SMEs, craft businesses and corporate sites in matters of process optimisation and the continuous improvement process.
In the t2informatik Blog, we publish articles for people in organisations. For these people, we develop and modernise software. Pragmatic. ✔️ Personal. ✔️ Professional. ✔️ Click here to find out more.