Lean Kanban in Change Management
Reliable results for difficult agile transformations
Does the following sound familiar? The agile transformation of your business has been going on for months or even years. You know that you will no longer set standards in dynamic markets without deep-rooted organisational improvements. Of course, you understand the essence of agility. You know that it’s not primarily about speed and efficiency but about delivering more valuable work packages in a better way, so they are created in smaller batches that can be evaluated sooner. The resulting faster feedback cycles ensure that less work runs in the wrong direction and there is less waste.
One of the primary goals is to establish an agile decision-making culture. Your employees should take on more responsibility and proactively find solutions for organisational challenges as well. You want at last to involve your people in a way that inspires them to deploy their full creative power. You also want to improve the flow of communication and build new bridges so that organisational units that have been operating separately now collaborate better.
As a result the teams are expected to significantly increase the value of their work. That includes non-functional quality improvements. And what’s more, an exploration of new business models, such as services that offer the customer novelty and considerable added value, is now also desired at the grassroots level. To make things happen, you are working hard on creating a company-wide sense of urgency to enhance and upgrade your value-creation streams.
So much for your wishes and ideas. And what does it look like in practice?
Daily reality
Reality looks very different in most organisations. Progress is faltering or non-existent. Although a considerable amount of time has passed, some things are even worse than in the past. And there is no exit from the trough of the J-curve. Bringing in new “agile change agents” may even have opened up a second J-curve trough. This means that the situation is not good and continues to deteriorate.
Employees moan behind the backs of their bosses about the “agility fad”, which to them is nothing more than old wine in new bottles. In their minds all this is just another initiative of the PMO to get the projects going, it has rarely brought advantages, on the contrary, it has almost always caused further slowdown. The prevailing feeling is that this is all about one thing: squeezing more output out of people.
Concerning an agile decision-making culture, the employees show little enthusiasm and prefer to wait for the decisions and impulses of their managers when new challenges arise. They are overloaded with work anyway, with endless task lists in which most tasks are high-priority. In addition, management decisions are often interpreted differently than intended by management, inadvertently or even deliberately so. Such “misunderstandings” sometimes only come to light after months. No one sticks their neck out. Everyone keeps their heads down.
Do classic change models help?
What to do? Are classic change models a solution? How about one of the popular change management models like Kotter’s 8 Steps, McKinsey 7S or Prosci ADKAR? Could we – under the leadership of a world-class change manager – finally become agile?
Unfortunately, this almost never works for agile transformations. All these change models focus on overcoming resistance that they consider to be in the natural order of things – which is indeed the case with these approaches, because these change models are based on a bundle of
- rules,
- processes,
- practices,
- structures,
- roles,
- and sometimes also values,
all of which are meant to be “implemented”, i.e. they are imposed on the staff without the employees being involved in solution-finding, design and decision-making.
These top-down approaches inevitably lead to resistance, misunderstandings, delays and furthermore to design errors (e.g. those caused by details of the real-life context not being appropriately considered), which then are detected too late or not at all if the change model itself does not run according to agile principles. In any case, the result is high costs and inertia. In most cases even the best change managers do not achieve more than pro-forma compliance, since the employees have already endured a number of similar change initiatives and “know” that the actual work can only be done to a large extent outside the new rules anyway.
The problem of selling change
No matter how well you sell this kind of external solution to your organizational challenges (here: a predefined “agility”), you will not touch the emotions of your employees. Overall commitment remains as it was, mostly at the level of “we simply do what we are told, thinking outside our role and job descriptions only hurts”. According to the well-known G12 Gallup study of 2018, this is the mindset of an average of 66% of all employees across cultures, industries, company sizes and continents.¹
A classic “change initiative” buzz does not advance agility in an organisation. It does not usually create added value, neither does it evoke identification or a genuine sense of purpose. In short, it doesn’t give people a reason to get out of their office seats. At the same time agile and inspired companies are gaining more and more advantage and creating new niches and markets for themselves with high margins.
The alternative to classic change management
Are there systems of change management that are better than the classical formula? Yes, there are a few: one of them is the Lean Kanban model based on the work of David J. Anderson.
Lean Kanban is a change accelerator and results booster. While Lean Kanban can also be seen as a change management model, it differs fundamentally from the classic approaches mentioned above in that it is not disruptive, because it begins with the status quo, i.e. with the state of things as they are. The existing structures, processes, roles and job titles are not challenged at first. Instead, plain reality is visualised in a smart way, thereby revealing and clarifying
- inconsistencies in the process,
- bottlenecks,
- idle times,
- lead times,
- capacity and quality issues,
- the availability of much-needed skills.
Improvements are quickly identified and tested. And the success of those measures becomes visible and generates quick wins.
The process of introduction Lean Kanban
Improvements are rather small at first, but then increasingly frequent successes gradually lead to ever more profound changes. The measures are worked out and decided on by all those affected and responsible and thus are fully supported right from the start. Lean Kanban inevitably promotes values such as transparency, mutual understanding and respect. Misunderstandings and a lack of buy-in are practically eliminated due to the high degree of participation and commitment. Even colleagues who would prefer to follow other routes in some areas can commit themselves to temporary experiments. All involved execute without friction or delays. There is no need for further change management.
As a first step, work flows are analysed systemically. Lean Kanban summarizes this with the acronym STATIK:
STATIK = Systems Thinking Approach to Introducing Kanban
The purpose: To create a Kanban system design, with the overall system in mind, to increase the value flow to the customer.
- Identify the services of a business unit. In what form are they “fit for purpose“?
- What are the causes of unsatisfactory deliveries?
- Nature and origin of requirements (“demand”)?
- What is the current delivery capability?
- Model the services workflow.
- Define appropriate service classes.
- Design the Kanban system.
- Coordinate the overall design with interfaces and stakeholders.
In this way work processes within value streams become visible across interfaces. A particularly interesting aspect of the STATIK approach is the relationships between system components. The transitions between process states are governed by explicit policies. The Kanban board is a modelling and management tool whose columns reflect crucial procedural steps. In addition, WIP (work-in-progress) limits are jointly defined for the columns, sometimes also for rows (“swim lanes”), and are regularly adjusted for ongoing optimization of the value flow.
Isn’t that just Kanban, as we already know it?
The Kanban board is not the starting point of the Lean Kanban model but merely a tool – albeit an important and necessary one – that supports the Lean Kanban practices effectively and efficiently. Below is a list of the principles and practices of Lean Kanban without describing all of them in detail in this article.
4 Basic Principles
- Start with what you do know.
- Agree to pursue evolutionary change.
- Respect current processes, roles, responsibilities and job titles initially.
- Encourage acts of leadership at every level in your organisation – from individual employees to senior management.
6 Core Practices
- Visualise.
- Limit Work-in-Progress (WIP).
- Manage flow.
- Make policies explicit.
- Implement feedback loops.
- Improve collaboratively, develop the system experimentally (using models and scientific methods).
By the way: Lean Kanban can be integrated into other process models – e.g. Scrum – and furthermore provides excellent support for scaling and enterprise service management of the entire organisation. The same applies to portfolio management at operational, tactical and strategic levels.
Practical examples
Example 1: Lean Kanban is often applied to control customer lead time so that customers get what they need at the right time. For this purpose, high-quality work packages (“doing the right thing”) are passed through the system smoothly (“doing it right”). The start times are chosen appropriately, not too early and not too late. This reduces multitasking and thus “switching costs” for the doers. At the same time this ensures that execution considers the most current state of learning.
Example 2: Timely and appropriate validation is often a challenge, as top-class experts from the specialist departments are rarely willing to spend much time on it. If validation is too slow and “fitness for purpose” of deliveries is not ensured, errors pile up unnoticed (in requirements engineering as well as in development), which have to be identified and corrected at a later date. This entails a lot of extra work, which is highly frustrating for all involved. We have observed IT organisations where, for months on end, more than 70% of the developers’ capacity was taken up in analysis and re-engineering meetings in which defects and misunderstandings produced a long time ago were first identified and then redesigned. During these periods the developers couldn’t produce any new features at all. Waste can have tremendously damaging effects when validation flow is managed poorly.
Example 3: Kanban board with congestion in validation
The things that, from a traditional developer’s point of view, do not fall within the developers’ area of responsibility (“if the relevant department does not manage to validate in time, then it is its own fault”) increasingly generate misalignment at earlier stages in the process, because assumptions are not properly validated. Thus analysts and developers unknowingly produce errors and the technical debt grows exponentially over time. At some point an avalanche of re-engineering and coordination meetings rolls in, blocking any new development for a long time. In addition, technical debt continues to grow, unnoticed, in these meetings. Of course, all this does not happen out of sloppiness but is the result of a wrongly constructed system. Work becomes increasingly unsatisfying. Developers don’t get to do the things they do best and enjoy most. Added collateral damage stems from the fact that at some point good people with high domain expertise leave the organization. It can hardly get more expensive for a company.
And what happens when companies use Lean Kanban? It inspires all stakeholders to improve flow and increase value. Instead of finger pointing at the specialist department (“they never have time anyway”), new ways are found to simplify and speed up validation. We’ve seen how developers have interactively helped power users and decision makers during the validation process, thus enabling them to validate complicated features much faster. At the same time additional learning effects on both sides improved the system’s overall capabilities. As a result of the accelerated validation flow the value of deliveries increased enormously, which the customers happily acknowledged. Their newly won satisfaction generated awareness of the high value of deep collaboration, challenging and co-creating intensively, continuously and right from the start. With tangible results of this kind, sponsors on the customer side have occasionally surprised us with an additional budget for new high-value features, as the high return on investment has become clear to them.
Advantages of Lean Kanban in change management
With a Lean Kanban approach the causes of suboptimal results become visible to everyone. Managers, technical experts and “external” stakeholders, such as customers and users, jointly recognise what can be done and what happens when the system is not improved. The participants design measures, conduct controlled experiments and enjoy quick results.
Lean Kanban evolution yields success in the form of
- faster flow,
- more innovative and higher quality solutions,
- higher customer satisfaction,
- visible progress,
- more recognition,
- less multitasking,
- more focus
leading to increased job satisfaction, from which the joy of change arises almost by itself, as well as more engagement and commitment and a heightened sense of responsibility.
These are precisely the effects that are difficult to achieve with classic change management. And in the usual agile transformations, too, this spirit is missing in 86% of the cases. Because according to a McKinsey survey, this is precisely how often digital transformations fail on average.²
Almost everywhere there is a lack of real participation, of commitment, of buy-in. Most of those affected have their feet on the brakes when it comes to change. This is, by the way, an aspect of human behaviour that we are all familiar with: we don’t like to change routines that we have been practising for years, even if the results become less and less useful – and we become even more resentful if someone orders the change without even asking our opinion beforehand.
Conclusion
Lean Kanban provides all the ingredients for successful change: shared experience of a transparent ACTUAL state and of the challenges, opportunities and possibilities that arise. This is followed by the joint design of improvements by management, experts and workers alike. No more “we came up with that and from now on, you’re doing it like this”.
In addition, change happens in small steps. Small changes are fail-safe, because you can roll them back without distressing service delivery. At the same time, even subtle changes can have huge benefits.
The joy of change and the joint design of structures and processes experienced through Lean Kanban creates a feeling of pride, responsibility and community spirit and thus develops the skills required for genuine self-organisation. All this finally leads to a sound readiness to tackle even profound change. And that is why evolutionary transformation is so powerful. That is why the evolutionary approach of Lean Kanban removes blockages that still stand in the way of agile transformations in most companies.
In this way new systems are being created with much better capabilities and value output than is possible in classical structures. Organisational learning becomes effective in a previously unimaginable way. All this generates success for the company, increases market share, opens up new markets and can even develop new business models and implement them much faster and more successfully than was previously possible.
Notes:
Would you like to know more about evolutionary change à la Lean Kanban? “Kanban: Evolutionary Change Management for IT Organisations” by David J. Anderson will furnish you with valuable insights. The book contains conclusive case studies, for example on organisational units at Microsoft, Motorola and Corbis. Incidentally, the Lean Kanban principles are now also being applied successfully in non-technical business areas. With the know-how provided by the book alone you can already achieve astonishing results. If you wish, trained Lean Kanban experts can help you make the transition to your high-performance culture faster and easier.
[1] Gallup G12 Study: https://www.gallup.com/q12/
[2] McKinsey Study (updated April 2019), Five moves to make during a digital transformation:
https://www.mckinsey.com/capabilities/mckinsey-digital/our-insights/five-moves-to-make-during-a-digital-transformation
This study also provides valuable information on what details are important.
Here you can find more information about Kanban.
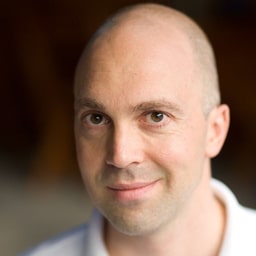
Hartmut Goetze
Hartmut Goetze helps companies achieve the results they strive for: outstanding business value, enthusiastic customers and market success. He is inspired by the dual goal of multiplying value creation and doing so in a humane way that is focused, motivational, highly effective and less stressful. His overriding aim is to improve the quality of life and commercial success of his customers.