Was eine alte Honda über Innovation verrät
Manchmal beginnt eine Entdeckungsreise mit einer scheinbaren Kleinigkeit. Für mich war es eine 50 Jahre alte Honda vor einem Biergarten in meiner Heimatstadt. Dieses Motorrad führte mich auf die Spur von Hondas faszinierender Geschichte – eine Geschichte, die zeigt, wie das Streben nach Perfektion und Effizienz Innovation hervorbringen kann.
Die sieben Muda: Hondas Kampf gegen Verschwendung
Im Kern von Hondas Erfolg steht das Streben nach Effizienz. Eine der Schüsselideen ist die Eliminierung der „sieben Muda“, also der sieben Arten von Verschwendung. Sie zielen darauf ab, Ressourcen sinnvoll zu nutzen und Verschwendung auf allen Ebenen zu minimieren. Besonders in der Fertigung haben sie eine enorme Bedeutung erlangt, aber die Prinzipien können ebenso in andere Lebensbereiche übertragen werden.
Die sieben Muda umfassen:
- Überverarbeitung: Dies tritt auf, wenn ein Teil oder ein Produkt über den notwendigen Standard hinaus bearbeitet wird. Obwohl dies wie ein Zeichen für hohe Qualität wirken mag, führt es oft zu unnötigem Mehraufwand an Zeit, Energie und Ressourcen.
- Überflüssige Bestände: Zu viele Vorräte binden Kapital und Platz, erhöhen das Risiko von Materialverfall oder Beschädigungen und können die Flexibilität eines Unternehmens stark einschränken.
- Transport: Unnötiges Bewegen von Materialien zwischen oder innerhalb von Standorten kostet nicht nur Zeit, sondern erhöht auch die Wahrscheinlichkeit von Beschädigungen und ineffizienter Nutzung von Ressourcen.
- Überproduktion: Mehr zu produzieren, als aktuell benötigt wird, verursacht zusätzliche Lagerkosten, erhöht das Risiko von Produktveraltung und blockiert wertvollen Lagerplatz.
- Warten: Wenn Prozesse nicht harmonisch aufeinander abgestimmt sind, entstehen Leerlaufzeiten für Mitarbeiter und Maschinen, die produktiver genutzt werden könnten.
- Fehlerhafte Teile: Jede fehlerhafte Komponente bedeutet nicht nur verlorene Ressourcen, sondern auch Zeit- und Kostenaufwand für Nachbesserungen und potenziell unzufriedene Kunden.
- Ineffiziente Prozesse: Standardisierte Arbeitsweisen sind wichtig, aber veraltete oder unpraktische Abläufe können kleine Ineffizienzen systematisch vervielfachen und langfristig enorme Kosten verursachen.
Die sieben Muda legten den Grundstein für viele der Produktionsmethoden, die Honda später zu einem Weltmarktführer machten.
Die Anfänge von Honda: Not macht erfinderisch
Soichiro Honda gründete 1937 das Unternehmen „Tōkai Seiki“ zur Herstellung von Kolbenringen. Doch die Herausforderungen ließen nicht lange auf sich warten: Ein amerikanischer B-29-Bomber zerstörte 1944 das Werk in Yamashita, und das Werk in Iwata stürzte 1945 beim Mikawa-Erdbeben ein. Hondo verkaufte die Überreste seiner Firma für umgerechnet 3.000 Dollar.
Aus der Asche wurde 1946 das Honda Technical Research Institute gegründet. Ohne Kapital war Honda jedoch gezwungen, nur das zu produzieren, was sofort verkauft werden konnte. So wurde Hondas „Typ A“ lediglich von 12 Personen in einer winzigen Werkstatt von 16 Quadratmetern gebaut. Es gab nur Platz für die Teile, die gerade bearbeitet wurden, was sich als Vorteil erwies, da die Nachfrage im Nachkriegsjapan sehr gering war. Der Versuch, in großen Mengen zu produzieren und auf einen umkämpften Markt zu drängen, hätte zum Bankrott geführt. Honda war gezwungen, sich auf die Nachfrage der Verbraucher zu konzentrieren und Motorräder „just in time“ zu produzieren, ein Ansatz, der später zum weltweiten Industriestandard wurde.
Die 5S-Methodik: Ordnung für Effizienz
Eine effiziente Produktion wie die Just-in-Time-Methode erfordert ein Arbeitsumfeld, das klare Strukturen bietet und frei von unnötigem Ballast ist. Nur so können die Prozesse reibungslos und fehlerfrei ablaufen. Hier setzt die 5S-Methodik an, ein System zur Schaffung von Ordnung, Sauberkeit und Disziplin am Arbeitsplatz, und eine wesentlichen Grundlage für kontinuierliche Verbesserungen.
Die 5S stehen für:
- Seiri (Aussortieren): Alles Unnötige entfernen.
- Seiton (Ordnen): Werkzeuge und Materialien dort platzieren, wo sie benötigt werden.
- Seisō (Sauberkeit): Sauber halten und Unordnung sofort erkennen.
- Seiketsu (Standardisierung): Klare Standards schaffen.
- Shitsuke (Disziplin): Eigenverantwortung jedes Mitarbeiters für Ordnung.
Dieses System macht es leicht, Abweichungen und Verbesserungsmöglichkeiten sofort zu erkennen und unmittelbar auf das nächste Bauteil anzuwenden.
Ein beeindruckendes Beispiel dafür ist die Entwicklung der Honda CB 400 Four: Bei der CB 350 wurde ein Schwingarm mit einer Platte verschweißt, um die Achse zu halten, was bis dahin Industriestandard war. Beim CB 400 Four bemerkte ein Linienarbeiter jedoch, dass das Teil konisch war und einfach in die Trägerplatte gepresst werden konnte. Honda implementierte diese Änderung sofort.
Ein anderes Beispiel ist die kleine Halteschlaufe am Bremspedal. Ein Testfahrer hatte sich den Fuß zwischen Bremspedal und Motorgehäuse eingeklemmt und schlug vor, eine Schlaufe anzubringen. Später blieb ein anderer Testfahrer mit seinem Hosenbein in der Schlaufe hängen, woraufhin er empfahl, die Schlaufe zu vergrößern und das Pedal 4 mm weiter vom Motor entfernt anzubringen. Dies wurde ab Motor Nr. 1084315 umgesetzt.
Und ein drittes Beispiel: Mit meinen 1.90m finde ich die hinteren Fußrasten und den niedrigen Lenker etwas beengend. Hondas nordamerikanisches Marketingteam bemerkte dies ebenfalls. Ab Fahrgestellnummer 1056883 bot Honda weiter vorne liegende Fußrasten und höhere Lenker an.
Hondas Ansatz zeigt, dass kontinuierliche Veränderungen helfen, um den Bedürfnissen von Kunden noch besser gerecht zu werden.
Kaizen und die 5-Why-Methode
Das ständige Hinterfragen des Status quo ist Teil einer Philosophie, die sich Kaizen nennt. „Kai“ bedeutet kontinuierliche Veränderung und „Zen“ bedeutet zum Besseren. Ein Modell wie die CB 400 Four kontinuierlich zu verbessern, mag manchem aufwendig erscheinen, aber diese Philosophie trägt dazu bei, dass das Modell auch fünf Jahrzehnte nach seiner Markteinführung mit einer bemerkenswerten Zuverlässigkeit glänzt. Und wenn Probleme auftraten, griffen Honda und seine Mitarbeitenden auf die 5-Why-Methode zurück – auch bekannt als 5 Whys oder 5 Warums.
Der Motor rasselt.
- Warum? Weil die Steuerkette locker ist.
- Warum? Weil der Steuerkettenspanner klemmt.
- Warum? Weil die Kette Drehpunkt des Spanners gerieben hat.
- Warum? Weil der Fahrer die Kette nicht ausreichend gespannt hat.
- Warum? Weil sich der Zugang direkt hinter dem Reifen befindet, wo er leicht verstopft, und die meisten Besitzer den Wartungsplan nicht einhalten.
Beeindruckend, wie Honda mit den fünf Warum-Fragen zur Ursache eines Problems vordringt und es löst. Liegt die Ursache eines Problems jedoch beim Motorradfahrer, z. B. wenn er unachtsam ist, ist Honda so offen, das betreffende Bauteil durch ein anderes zu ersetzen, das der menschlichen Natur mehr entspricht, wie z. B. die weniger fehleranfälligen Spanner der CB 650.
Fazit
Zusammenfassend zeigt die Geschichte von Honda, wie Innovation aus einer Notwendigkeit heraus entstehen kann. Die Prinzipien der Just-in-Time-Produktion, die 5S-Methodik und Kaizen – das Streben nach kontinuierlicher Verbesserung – bildeten die Grundlage für den Erfolg von Honda. Durch die Eliminierung von Verschwendung (die sieben Muda), die Konzentration auf Effizienz und Qualität und die ständige Herausforderung des Status quo hat Honda eine Unternehmenskultur geschaffen, die ihresgleichen sucht.
Die Anwendung der 5-Why-Methode zur Ursachenanalyse von Problemen und die schnelle Umsetzung von Verbesserungsvorschlägen zeigen, wie wichtig Flexibilität und Detailgenauigkeit in der Produktion sind. Honda hat bewiesen, dass selbst kleinste Optimierungen – von ergonomischen Anpassungen bis hin zu Designänderungen – langfristig einen großen Einfluss auf die Zuverlässigkeit und den Erfolg eines Produkts haben können.
Letztendlich lehrt uns der Ansatz von Honda, dass Disziplin, Innovationsgeist und die Einbeziehung der Mitarbeiter auf allen Ebenen entscheidend sind, um ein nachhaltiges und erfolgreiches Unternehmen aufzubauen.
Hinweise:
Wollen Sie Ihr Unternehmen so entwickeln, dass es Nutzer, Kunden und Entwickler wirklich inspiriert? Dann vernetzen Sie sich einfach mit Benjamin Igna auf LinkedIn und finden Sie ein Vorgehen, das genau zu Ihnen und Ihrem Kontext passt. Alternativ können Sie auch auf Stellar Work zugehen.
Wenn Ihnen der Beitrag gefällt oder Sie darüber diskutieren wollen, teilen Sie ihn gerne in Ihrem Netzwerk. Und falls Sie sich für weitere Tipps aus der Praxis interessieren, dann testen Sie gerne unseren beliebten Newsletter mit neuen Beiträgen, Downloads, Empfehlungen und aktuellem Wissen. Vielleicht wird er auch Ihr Lieblings-Newsletter.
Benjamin Igna hat drei weitere Beiträge im t2informatik Blog veröffentlicht:
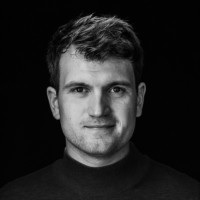
Benjamin Igna
Benjamin Igna ist Gründer und Berater bei der Stellar Work GmbH. Er hat Transformationsprojekte erfolgreich geleitet und komplexe Projekte in den Bereichen Automobil und Technologie gemanagt, wobei er stets den Fokus auf messbare Ergebnisse und operative Effizienz legte. Seine Expertise liegt darin, Strategie und Umsetzung in Einklang zu bringen, um nachhaltiges organisatorisches Wachstum zu fördern.
Zudem ist er Gastgeber des Podcasts “Stellar Work”. In jeder Episode beleuchtet er bemerkenswerte Persönlichkeiten, die die Grenzen des Produktentwicklungsprozesses neu definieren.
Im t2informatik Blog veröffentlichen wir Beträge für Menschen in Organisationen. Für diese Menschen entwickeln und modernisieren wir Software. Pragmatisch. ✔️ Persönlich. ✔️ Professionell. ✔️ Ein Klick hier und Sie erfahren mehr.